Projects
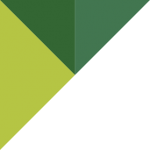
View Our Projects
Gisborne District Council Building
This project involved the demolition of 3 two story buildings. An asbestos survey was carried out and the ceilings and floors proved positive as asbestos containing along with the roofing and cement sheeting on the exterior. Prior to demolition the asbestos team removed all asbestos identified in the survey. During soft strip of the buildings more suspected asbestos material was identified, work was halted, and control measures put in place, samples of all the suspected materials were taken and later identified as asbestos containing. A new asbestos removal control plan was drafted along with an updated SSSP and immediately put in place. Demolition of the building was put on hold until all identified asbestos had been removed. Our asbestos team remained on site during the demolition phase of works in case any further suspected materials be identified.
Ballance Agri-Nutrients
Ceres New Zealand were chosen as the preferred contractor for the asbestos removal and demolition of 4 buildings at the Ballance Agri-Nutrient’s factory in Whangarei. The works involved the removal of over 11,000m2 of asbestos super six roofing and cladding, demolition of all structures to ground level as well as demolishing the 40-metre-high chimney. There were also numerous quantities of fertilizer throughout the factory which had to be cleaned prior to gaining any independent assessor clearances. The heights of each building varied with the highest at approx. 25 metres high. To remove the asbestos roofing and side cladding we attempted to source a large enough elevated work platform but were unable to get one in NZ. We then went with the methodology of crawler crane with a man basket to enable safe access.
201 Port Road
Ceres New Zealand were chosen as the preferred contractor for the asbestos removal and demolition of the former Fertilizer Factory in Port Road, Whangarei. The works involved the removal of 6,000m2 of asbestos super six roofing and cladding. There were also numerous quantities of fertilizer throughout the factory which had to be cleaned prior to gaining any independent assessor clearances. There were fragments of asbestos debris located to the perimeter of the building, these were first cleaned by carrying out a hand/emu pick of any visible debris by spraying them and then placing into asbestos waste bags. The integrity of the building was also checked as staff made their way around the building and any breaches were covered with plywood. Once the outside was completed the interior needed to be cleaned out of remaining chattels etc. to enable full access to the asbestos super six roof. This was carried out using a bobcat with a fork attachment for palleted materials and the bucket attachment for any general debris. This was all loaded out into waste bins using the bobcat. The floor was then fully cleaned to enable a clean working area. Once all the above was competed, roof removal works could commence. Operatives encapsulated the roof sheets using an ABC encapsulating paint/water mixture which would bond any loose fibres to roof sheets. All roof removal took pace from inside the building by EWPs. The last stage of asbestos removal works was to remove the asbestos side cladding. This was carried out by EWP and utilised the same methodology as the roof by bonding and removing. Once clearance was given by the independent assessor, deconstruction works could commence. Starting at the east end of the site the first building was demolished and loaded out on a regular basis to avoid material/debris build up on-site. All slabs below the buildings were to be kept until testing of any possible heavy metal or other contamination could be identified.
Fletcher Reinforcing
This project involved the removal of 1,200m2 of asbestos “super six” roofing and cladding along with 400m2 of bitumen/butanol roofing materials. Contaminated soil was discovered as the project progressed and Ceres were asked to remediate the soil. The soils were located adjacent to a railway track with daily movements of trains through the area. Works were stopped when this occurred and regular inspections of the tracks to ensure no debris was on the track lines and all access gates were locked off to keep out any unauthorised personnel. The asbestos “Super Six” roofing was at a height of 18 metres at the peak of the roof. To minimise the risk of working at height an internal scaffold birdcage platform was erected inside the building which would enable the roof sheets once removed to be lowered down onto the platform and then taken to ground level by MEWP. All staff were wearing harnesses attached to static lines as further protection for falls from heights. The roof sheets were bonded and prior to removal and care was taken not to overload the EWPs due to the height. Background monitoring was conducted during all aspects of removal works and the control measures implemented by Ceres resulted no elevated fibre release. For the removal of the bitumen roofing, handrails were erected around the flat roof and access was set up by a temporary scaffold staircase for personnel and waste movements. The bitumen roofing was bonded and then removed using scrapers and loaded in to one-ton bags, which were then lifted from the roof using an excavator and loaded directly into an asbestos waste skip.
Waitakere Hospital
Waikune Prison
Yarrow Stadium
Blair Tenant Hostel
The project involved remediating a former university hostel building which had been derelict for almost 10 years. Due to various fires and squatters the building was in a state of disrepair and careful access was required for some areas. The external parts of the building contained asbestos cement and cement soffits along with having to carry out an emu pick of the exterior grounds from vandalized asbestos sheets. Inside the building asbestos cement was discovered to the corridor ceiling panels along with the bathroom cement interior. All asbestos was successfully remediated, and the project was completed in 4 weeks.
Invercargill CBD Redevelopment
New Dunedin Hospital (Cadbury’s)
Ceres New Zealand were the preferred contractor by the Ministry of Health for the demolition of the 35,000m2 former Cadbury’s Factory and adjacent buildings to make way for the New Dunedin Hospital.
The works involved a full strip out of the building as well as asbestos removal, lead paint removal and demolition/deconstruction of the structures. The demolition/deconstruction is due for completion in September 2021 before Ceres New Zealand begin the foundation removal, groundworks, and piling.
University of Otago – Dental School (Two Stages)
The project was awarded to Ceres NZ in April 2016 and was complete by mid-July 2016. The demolition project was a part of the enabling works of a multi-million-dollar dental school redeveloped works at University of Otago in Dunedin. The project involves demolition of 5 story concrete adjoining the main building. The project also involved removal of asbestos, demolition of 2 smaller buildings and adjacent building protection. All the work was completed in a live educational campus environment. During the strip-out and asbestos removal phase, additional asbestos was uncovered. Ceres took all necessary steps to safely remove the newly found asbestos containing materials. Ceres NZ employed additional resources to expedite the additional works and kept the project on-schedule for completion in mid July 2016. Working in a live school environment controlling dust, trucks, and noise in the middle of the University. A strong and effective co-ordination with the University authorities, Project Management team, City Council and Ceres NZ ensured an efficient Traffic Management System. Any disturbance to the day-to-day activities of the University was communicated well in advance to minimize disruption.
Tahuna Pavilion
The Tahuna Pavilion decontamination project was put up for tender on behalf of Dunedin City Council and Ceres NZ LLC were successful in their proposal.
The project involved an initial environmental fine clean & detail of the interior which was discovered to contain asbestos dust which was a direct result of the delaminating “super six” roofing above.
Once the internal works were completed the roofing was removed utilising MEWPs and encapsulating the roof sheets prior to removal using an asbestos encapsulating paint.
There were numerous materials stacked outside the perimeter of the building which had been placed there over the previous few years and were all to be sent away as contamainted waste.
Once the initial exterior clean-up was completed the outer perimeter required a soil scrape from asbestos in the soil which was discovered and successfully remediated.
The roof area of the building was around 1,050m2 and was completed in 6 weeks a week ahead of schedule.
Dunedin Railway Station
Ceres New Zealand were approached by Feldspar on behalf of the Dunedin City Council to carry out remediation works to Dunedin Railway Station after an asbestos survey had been carried out prior to refurbishment works taking place. The survey revealed asbestos dust from swab samples taken which were due to historical maintenance work on pipework which had previously been removed. To enable safe access to the ceiling space a fixed scaffold staircase and platform was erected with a ladder on the platform to access the area, scaffold boards wrapped in 1000-gauge polythene were utilised as walk boards for areas without a walkway. A full enclosure was constructed around the scaffold and all vents and penetrations were sealed prior to remediation works commencing. All batts and insulation materials to pipework, air handling units and calorifiers was sprayed, removed, and placed into asbestos waste bags as contaminated waste as it would not be possible to decontaminated due to the nature of the product. A full environmental fine clean & detail was carried out utilising a combination of “Hepa” type vacuums, takrags and wet wipes were used to ensure no dust/debris remained. Background control monitoring was carried out by an independent assessor during all aspects of the removal works to ensure compliance that all ambient air levels were below the control limit of <0.010 f/ml. Once all remediation works were completed the enclosure underwent a four-stage clearance by an independent assessor who carried out a visual examination, took swab samples and finally carried out re-assurance air monitoring within the enclosure and once all clear was given back to a very happy client.
Christchurch Police Station
The former Christchurch Police Station building was in Christchurch’s central business district. The demolition of the 16-storey building was performed using implosion. The project involved service disconnections, asbestos removal, soft strip works, hard demolition, foundation removal and engineered backfill upon completion. During the project, additional asbestos was discovered. The date for implosion was fixed months ahead, therefore it was critical to maintain schedule despite additional asbestos removal. With pro-active engagement with the community, neighbouring businesses and Christchurch City Council, Ceres NZ managed to complete the implosion perfectly. Due to significant land contamination beneath the foundations, Ceres NZ engaged a contaminated land specialist to provide advice on the efficient remediation for this land.
Firestone Factory
Ceres NZ was preferred contractor for asbestos removal and demolition of the former Firestone Factory in Papanui, Christchurch. This large-scale project involved demolition and removal of asbestos from 25,000m2 structure. A challenge was safe demolition of the factory roof, one-third of which contained a highly friable asbestos-containing sprayed coating. There was also asbestos pipework, cladding, gaskets and asbestos dust and debris throughout the factory. Soil testing of the adjacent paddock areas identified asbestos contamination to the soil which also required remediation.
To deliver the demolition and asbestos removal works, our team devised a methodology based on a staged approach. This was essential given the sheer size of the structure, and enabled works to be performed safely to a consistently high standard. The is outlined below:
Asbestos Removal
- Removal of all redundant pipework and equipment
- Removal of roof using Foamshield as an asbestos fibre suppressant
- Independent Asbestos Clearance in a staged approach.
Demolition
- A 45-ton demolition excavator was used to demolish the higher levels of the factory
- A 20-ton demolition excavator was used to demolish the steel structure
- A 30-ton excavator was used for the foundation and slab removal
Contaminated Soil Removal
- The slabs and foundations were removed in a staged approach to avoid uncovering any contaminated soil
- An environmental consultant was engaged to provide advice on the remediation
- Based on the sampling and test results, contaminated soil was removed and disposed at accredited disposal sites.
CDHB Car Park & Sexual Health Building
The 5-storey hospital car park was damaged during the Canterbury earthquake events and subsequently demolished by Ceres NZ to allow for future hospital development. The car park was in Christchurch’s CBD, surrounded by active footpaths, bus lanes and roads. The entire project was completed in less than 3 months and included cut and crane, high reach demolition and site clearance.
The scope of work included:
- Cut and Crane bays adjacent to the laboratory
- Service disconnection
- High reach demolition
- Removal of foundations
- Backfilling
This project involved the removal of an asbestos adhesive which was below an asbestos roofing felt which covered an area of 519m2, also on the roof was an asbestos tar which was around 30mm thick in some places, this covered an area of around 280m2. There was also massive asbestos contamination to the underfloor area, which was around 2,500 tons of contaminated soil, the asbestos team worked in with the demolition team to ensure the contaminated soils were encapsulated so the building could be demolished to the ground floor slab and the soils removed by excavator and loaded out on to pre-lined asbestos waste skips, the contaminated soil works started in November 2016 and were finished in February 2017. Works are taking place in a high traffic pedestrian area with offices around 3 sides of the site. Ceres removed 1,013 tons of contaminated material from the underfloor area.
Hanger 4 – Christchurch Airport
This project required the removal of 5,500m2 of asbestos “super six” roofing and cladding along with a variety of internal cladding, lagging and vinyl products. The total weight of Asbestos Containing Materials and contaminated items came to approximately 280T. As the hangar was located directly adjacent to the airport’s regional walkway, at one point only 1.2 m between the Hangar and the walkway – Ceres employed robust removal techniques and stringent FOD (Foreign Object Debris) management procedures. Internal cement boards, ceiling panels, lagging and vinyl were removed initially and an asbestos clearance given for each section of the hangar. A soft strip of all internal materials including insulation was performed in order to clear a pathway for MEWPs to reach the roof height. A test removal of two bays of roofing “super six” clarified the best technique for removing the remaining material and eliminated any further need for working on top of the roof. The efficiency of removal increased quickly from the initial test section, hampered only but the self-imposed safety protocols to prevent any FOD. Engineered clamps were used on all exposed edges as removal progressed and a daily lockdown procedure included checking all existing clamps and adding extra support where needed depending on weather forecasts. All roofing materials were removed without incident and without FOD entering the airfield. The Hangar and ancillary buildings were then given a full environmental clean and given clearance in four separate sections. Demolition of the remaining structures were undertaken a night to reduce the potential impact of airport operations. Loading out of demolition materials was completed efficiently and the last section of work was two sections of contaminated soil identified during the environmental clean
QE2 Stadium
Ceres New Zealand were successful with the proposal for the Former QE2 stadium asbestos contaminated land remediation. Previous estimates for all the contaminated soil to be transferred to landfill was at a cost of around $9 Million NZD. Ceres NZ developed a methodology to screen the material and reduce the volume of contaminated material. By adopting this method, Christchurch City Council made a saving of approximately $6-7 Million. The footprint of the site was approximately 7 hectares. The project involved processing of approximately 25,000 cubic meters of Asbestos contaminated soil and concrete stockpile. The material processing included a screen, wash plant, filtration tank and a manual picking station. Most of the processed material was re-used on-site as a backfill.
Heberden Cluster
The Heberden Cluster consisted of the demolition of 14 houses along Heberden Avenue, Sumner, Christchurch. The project was completed in less than 3 months including asbestos removal, site clearance and top soil works.
The Scope of work included:
- Demolition of 14 houses
- Asbestos removal
- Vegetation removal
- Service disconnection
- Removal of retaining walls
- Topsoil works
The project area was in a cliff collapse and boulder inundation zone under the port hills of Christchurch. Most of the houses were close to the hill and had a high risk of falling debris. Ceres NZ completed the project within the allocated programme and budget.
Statistics House
The Statistics building at CentrePort, Wellington was structurally damaged during the November 2016 earthquake. CentrePort engaged Ceres NZ to demolish the building. This was a very complex demolition project due to:
- The building being structurally compromised
- Working near Strait NZ Bluebridge ferry operations, Customhouse and Pipitea Portacom Village
- Retrieving tenant servers and confidential documents from the building for destruction
- Existing services running into and surrounding the building
As the building was unsafe to enter, Ceres NZ undertook a “dirty demolition” and safely retrieved and destructed the servers and confidential information. CentrePort scheduled the demolition of Statistics House to occur during the 2017/2018 Christmas Break to minimize disruption for their staff and port operations. The Ceres NZ team were efficient and successfully completed the demolition safely and within programme. Due to extreme winds, the methodology was changed in consultation with the clients and structural engineers. All confidential documentation (papers, hard drives etc..) inside the building were destroyed securely. WorkSafe NZ also commented that they have never seen a cleaner demolition site. Ceres NZ completed the project as required by our client, Centreport. Even though the building was demolished as a dirty demolition, Ceres NZ managed to recover over 30% of the concrete and sent them for recycling.
Shed 19
The project involved demolition of a steel portal-frame structure shed on Waterloo wharf in Lambton Harbour in Wellington central. Concrete infill panels and steel cladding is used extensively on the exterior of the building. There’s an external gangway and elevator. The main features of this project included removal of asbestos, internal strip out works, demolition the steel portal frames, concrete wall cutting and removal on an old wharf where heavy machines are not allowed to work on. Due to the special location of this project, no heavy machines are allowed on the wharf, Ceres NZ managed to do all asbestos removal work and strip out work by hand only. As the windy weather in Wellington, safety scaffolding was constructed first to ensure the demolition work carry out safely. Also, all the concrete walls, nibs were broken out on site and removed by small pieces. Besides, Ceres NZ proposed cut & crane method by using a barge around the wharf with a crawler crane on it and remove the steel portal structure piece by piece which resolves the problem of removing heavy materials on a weak wharf. By using this method, Ceres NZ successfully demolished Shed 19 in scheduled time with low risk but high quality.
BNZ Building
Ceres NZ was awarded the contract for demolition of old BNZ building on the Wellington waterfront in June 2019. The building was built in 2009 and suffered damage during the Kaikoura earthquake in 2016. As the building is relatively new, most of the building materials can easily be reused. The following list details items we have will
retrieve, as part of our methodology, for recycling and re-use:
- External Glazing 7,300m2 – to be reused in Wellington Children’s Hospital
- and various commercial buildings
- Refrigeration units – to be reused in a hotel in Fiji
- Generators – will be reused by CentrePort
- Electric Boards – will be reused by CentrePort
- Insulation material
- Carpet tiles – 10,000m2
- Doors and windows
- Electrical cables and wires
- Scrap metal
- Lift gear
- Fire extinguishers.
The only building material which suffered water damage and does not comply to the current building code was sent to C&D landfill. Concrete debris was processed in the Port’s recycling yard and converted to crushed concrete for re-use in infrastructure projects. It is estimated (by weight) that 98% of the building will be recycled or reused by the end of the project.
61 Molesworth Street
The 8-storey building at 61 Molesworth St, Wellington was severely damaged after the Kaikoura earthquake. The Civil Defence and Emergency Management setup a cordon around the building and had to demolished quickly to allow the streets and neighbouring business to re-open. The mobilization of heavy demolition equipment from Christchurch was the primary challenge since State Highway 1 from Kaikoura to Picton was closed due to the slips. The demolition excavators had to be broken down and transported in number of trucks due to weight restrictions in Inland Road. The excavators were re-assembled in Wellington and was made available to work in less than a week after the earthquake. The methodology was developed taking consideration of all stakeholder’s interests including Wellington City Council, WorkSafe NZ, Schools, Neighbours and, Businesses. The building was built in early 1960’s and suspected to contain asbestos. Due to the nature of the damage to the building, workers were not allowed inside the building to remove asbestos prior to the demolition. Additional dust suppression, asbestos testing regime and constant air monitoring was set-up to monitor any asbestos contamination. The building was demolished in approximately 4 weeks using a CAT 385 high reach excavator and 3 demolition excavators. The cordon was reduced periodically, and final cordon was lifted by New Year. This project was completed under emergency conditions. Ceres NZ crew worked 14 hours a day, 7 days a week to complete this work. Wellington City Council wanted to the main Molesworth Street to be opened as quickly as possible. By the first week of Dec 2016, one lane of the street was open to public. The demolition work was complete by Christmas 2016, enabling all neighbouring properties to open. The contract, regulatory approval and mobilization was performed in record
time. The project was completed in less than 3 months with the High Reach Excavator and 2 demolition excavators. Despite inclement weather, the cordon was reduced to the building footprint before New Year’s Day. Ceres NZ managed to extract a heritage listed Mural from the ground floor much to the delight of the arts community. This mural was designed by renowned artist Jim Allen and weighed about 36 tonnes. To demolish a 7000-tonne concrete structure and still be able to save the mural speaks volume about the skills and precision of Ceres NZ team Ceres NZ mobilized all equipment from South Island in 2 days even though the State highway 1 was closed due to the landslips in Kaikoura. Ceres NZ coordinated with Wellington City Council, Service Providers, WorkSafe NZ and all neighbouring property owners for the safe and expedited demolition of the building.
Transpower HVDC Building
Ceres New Zealand LLC was contracted for the Deconstruction of Haywards Pole 1 Building by Transpower. The scope of works included asbestos cladding removal, demolition of the valve house and Control Building, Removal of C&D Debris, Crushing Concrete Debris, Backfilling the basement and Installation of Monitoring Wells.
A previous asbestos contractor carried out mercury cleaning and asbestos removal prior to the award of the demolition contract. Certain areas could not be removed of asbestos containing material during the initial works by the previous asbestos contractor and Ceres NZ LLC as the successful demolition tenderer were engaged to remove the remaining asbestos containing materials. Further sampling was carried out once works on-site had commenced and further asbestos containing materials were discovered. The following Asbestos was to be remediated; Exterior Cladding, Cement Sheeting, Environmental Clean of Dust/Debris to Internal Beams, Removal of Smoko Hut Roof, Exterior Roofing Membrane Below Flashings, Cement Wall Panels, Fire Doors & Switchboard Panels. During the remediation works background monitoring was carried out with 2x pumps placed around the work area and a 3rd pump placed at the boundary of the Transpower Haywards site and the nearby residential properties. This project involved the demolition of Pole 1 Building at Haywards HVDC Station for Transpower. The building was in the live sub-station area. A detailed planning was undertaken to eliminate all electrical hazards. Additional asbestos and mercury were found during the soft strip phase and was removed accordingly. The job was completed on-schedule despite additional hazardous materials removal work.
Tory Street Car Park
The Tory Street Carpark (also known as the Reading Cinemas carpark) complex on Tory Street, Wellington was in danger of imminent collapse due to damage sustained by the November 2016 Kaikoura earthquake. Ceres NZ negotiated the demolition contract with Naylor Love, who were the main contractors for this project. The site establishment was completed efficiently during the 2016 Christmas break, having carefully planned the logistics for equipment mobilization, to avoid disruption during the holiday season. Due to the damage caused by the earthquake, contractors were not able to access the building to strengthen the structure prior to the demolition. The adjacent buildings and services added some significant challenges. We decreased the risk of damaging surrounding buildings by hanging a debris screen from a crane. Our high reach demolition excavator successfully demolished the 7-storey carpark building in less than 3 months with minimal damage to neighbouring properties and no damage to any underground services.
Coldstores
Cold Stores at CentrePort Wellington building was about 10,000 square meters. Cold Stores comprised of 4 Cold Stores build close to king’s wharf. The buildings were deemed earthquake prone in 2016 and the decision was made to have them demolished. Ceres New Zealand were engaged in 2018 to provide deconstruction services. The cold stores were made of Polystyrene panels. The Ceres NZ demolition team assigned to this project recycled a significant amount of demolition waste including concrete, bricks, metal, and fixtures. Ceres NZ ensure that sustainability is at the forefront when handling demolition waste by utilizing their specialist equipment if
required. For this project, Ceres NZ invested in a polystyrene compressing machine which reduced the volume of expanded polystyrene by 40 times. The steel from the polystyrene was stripped and sent to scrap yard for recycling. The concrete debris was sent to Centreport’s recycling yard for processing into crushed concrete. The crushed concrete was re-used in the port infrastructure projects. Some items such as ovens, furniture, structural steel was salvaged and provided to the local clubs. The project generated 4,000m3 of polystyrene, but by processing this material using the specially procured compressing machine, only 10m3 of landfill space was used. Ceres NZ consulted with the Environmental Protection Authority (EPA) regarding all aspects of final disposal site and handling requirements.
Waitangi Wharf
Ceres New Zealand were engaged by the Memorial Park Alliance to cut and remove 25 concrete piles from Waitangi Wharf located on the Chatham Islands, as part of the $58m Waitangi Wharf Upgrade.
The Waitangi Wharf upgrade was considered a lifeline for the local community, due to its vital purpose as the Island’s only Port. The severely degraded wharf was built in the 1930’s to service the local community, but with import and exports increasing in recent times, the new port requires 9,500m2 of land reclamation.
Ceres New Zealand’s concrete cutting division designed an underwater hydraulic wire saw specifically for pile removal projects. This equipment delivers a safe and efficient method of pile removal, whereby the saw cage is lowered over the concrete pile by crane until it reaches the bottom. The operator then conducts a controlled cut from the wharf, barge, or land with the use of hydraulics. Once the pile is cut, the crane lifts the pile and wire saw cage from the water to the wharf or land where the pile is detached. The wire saw is then prepared for the next pile removal.